|
Development
of Packaging Converting-related Machinery
STRETCH
HOOD MACHINE SH-1 |
General
Description
The stretch hood machine packs palletized products.
A guesseted tubular film roll is drawn by a set length,
and the end is sealed to make a bag. The bag is
placed over palletized products to enclose them and
prevent collapse using the stretching force of the film.
Similar machines include film stretch wrapper (stretch
film is wound around the products) and shrink hood machine
(using heat-shrinkable tubes).
Model SH-1 uses just one film roll to pack products.
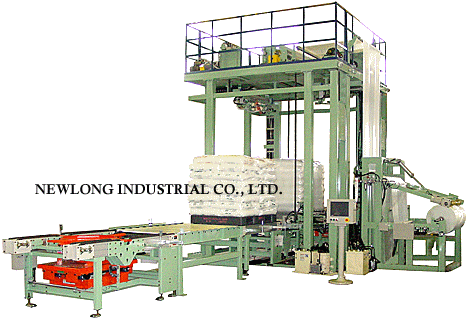
Features
1. Bag-like film covers the products so that the top
surface of the products on the pallet is also protected,
allowing open yard storage. (superior to stretch wrappers)
2. Heat-vulnerable products can be packed because
shrinking force of film is used to press the products.
(superior to shirink hood machines)
Specifications |
Capacity |
Nor.
90pal/h
|
Max.
package size
|
1450
(W) x 1250 (D) x 1600mm (H)
|
Film
size core dimensions
|
φ76mm |
Roll
width
|
Max.
1400mm
|
Roll
diameter
|
Max. φ
1200mm |
Power
supply circuit
|
3-ph,
200V, 50Hz/60Hz
|
Control
circuit
|
DC24V |
Power
requirement
|
Approx.
48kVA
|
Air
consumption
|
250NL/min
(at 90pal/h)
|
Air
pressure |
Min.
0.5MPa |
Operation
Procedure
1. Palletized products are transferred to the machine via
transfer conveyors. The system automatically detects
the height of the products with a sensor and determines
the neccesary length of film to pack the products.
2. The draw rollers pull one screenful of the film to the
lower end of the vacuum pickup.
3. Gusset sections of the film tube are pulled apart by
vacuum suction, then, opening arms which are individually
equipped with a clamp unit firmly grip the film tube at
its four corners.
4. Each clamp unit, keeping a firm hold of the film, moves
outwards in order to spread the film evenly over the
contour.
5. Four winder fingers, mounted on the extender, move
horizontally to the position where they can enter the
opened film and ascend up to the specified position.
The winder expands again to the size of the opening to
receive the film.
6. The winder rollers move toward the finers to hold the
film between the rollers and the fingers.
7. The draw rollers draw the film by the length
additionally required. The winder rollers haul in
the film and wind it around the fingers in the accordion
form.
8. When the film is sufficiently drawn, the rollers stop
and the film end is impulse-selaed and cut.
Temperature is controlled by the controller of the high
reply.
9. When a series of operations have been successfully
completed, the extender stretches to accommodate the
products with a good margin.
10. The extender descends, and the tucked film is unfolded
to cover the products. The winder rollers return to
the origin when the timer counts down from the start of
descending. (Please refer to the operation process
illustrated at the far right)
11. On reaching the pre-set position, the winder rollers
move to the fingers and hold the film to prevent it from
slipping off from fingers. Keeping this state, the
extender further descends to below the products and
releases the film, which is shrunk to smaller than the
product size. By this, the leading edge of the film
is securely pushed into the space below the pallet to
stabilize the products on the pallet.
12. The extender expands to clear the products and ascends
to the origin.
13. The packed products are discharged by the transfer
conveyor while the next products to be packed arrive at
the set position on the machine (return to step 1)
OUTWARD DIMENSIONS
|
|